Are Digital Twins Going to Fuel the Next Energy Revolution?
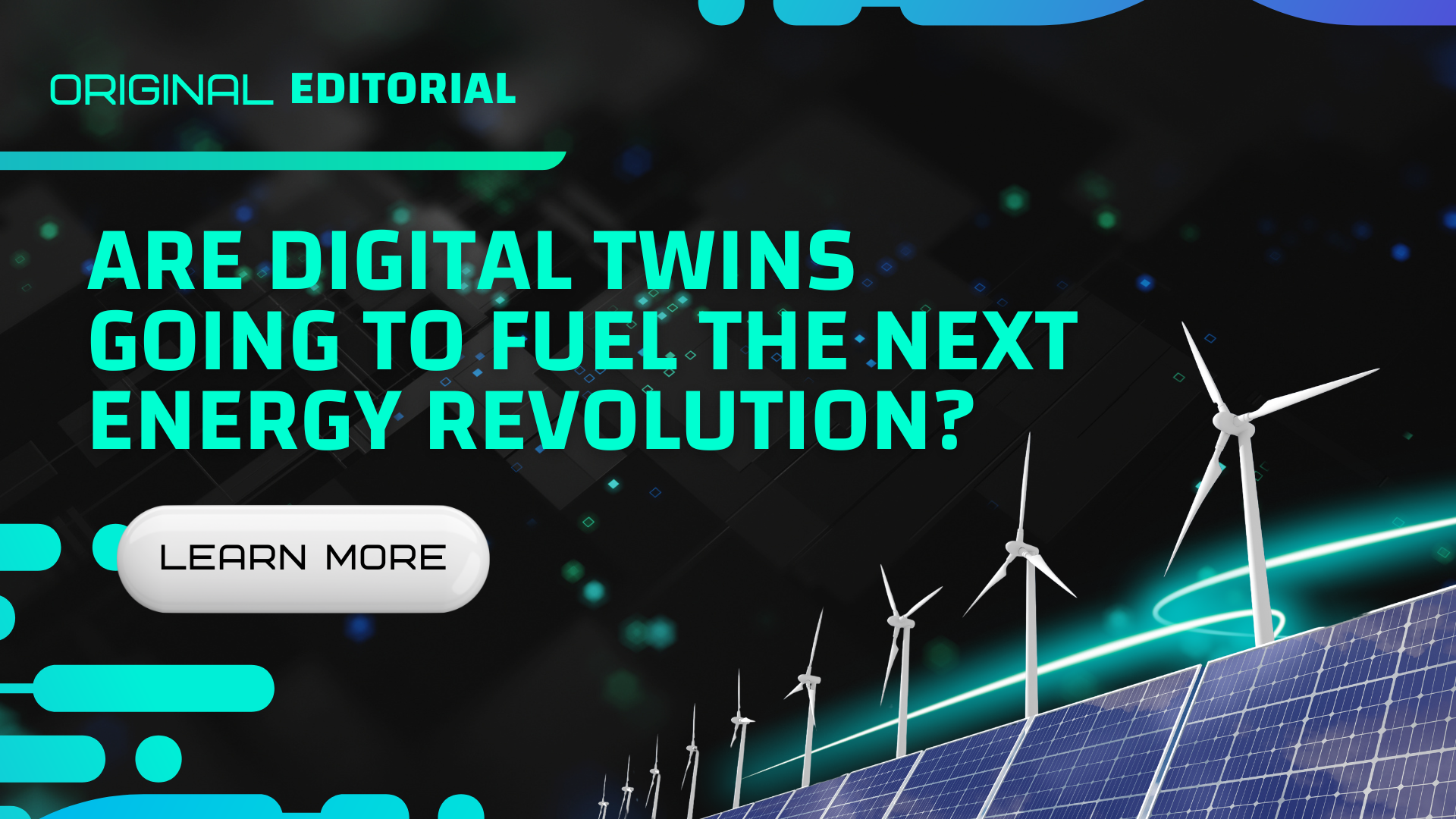
In the complex and capital-intensive world of oil and gas, the energy demand is soaring while the pressure to enhance efficiency, safety, and sustainability intensifies. Digital transformation, spearheaded by the concept of the "digital twin," is emerging as a key enabler in meeting these challenges. As the industry gears up for the World Advanced Manufacturing & Logistics Summit & Expo (WAM Saudi) in November 2024, let's delve into how these virtual replicas are reshaping oil and gas operations, ushering in a new era of optimised production, predictive maintenance, and risk mitigation.
A Necessity Born from Complexity
The oil and gas industry operates within a delicate balance of maximising production while navigating intricate operational landscapes and stringent safety regulations. Traditional methods often struggle to keep pace with the complexity of modern operations, necessitating innovative solutions that provide real-time insights and predictive capabilities. Enter the digital twin – a virtual counterpart of a physical asset, process, or system that serves as a dynamic, data-driven looking glass into real-world operations.
Illuminating the Unseen
In the oil and gas space, digital twins are typically created for critical equipment like drilling rigs, pipelines, refineries, and offshore platforms. By integrating data from various sources, including sensors, Supervisory Control and Data Acquisition (SCADA) systems (industrial control systems that gather and monitor data in real-time), and historical records, a digital twin offers a holistic and up-to-the-minute understanding of an asset's performance, health, and potential environmental impact.
This virtual replica is not just a static model; it's a living, breathing representation that evolves in tandem with its physical twin. It empowers oil and gas companies to:
·Gain profound insights into operational performance: By simulating various scenarios and analysing real-time data, digital twins help identify bottlenecks, optimise processes, and predict potential failures, leading to improved efficiency and reduced downtime.
Make proactive, data-driven decisions: The digital twin provides a virtual sandbox for experimentation and optimisation without impacting real-world operations. This facilitates informed decision-making, risk mitigation, and cost reduction.
·Bridge the gap between the physical and digital worlds: By creating a seamless connection between real-world assets and their virtual counterparts, digital twins foster a new era of operational intelligence and agility.
The Paradigm Shift of Operational Efficiency
Digital twins are fundamentally transforming the way oil and gas companies operate.
Predictive Maintenance Becomes Proactive
Traditional maintenance strategies in the industry have typically been reactive, meaning equipment is repaired after it fails, or scheduled based on fixed time intervals regardless of the machinery's actual condition. Both approaches are inefficient and costly.
Digital twins revolutionise this paradigm by enabling predictive maintenance. Through real-time data analysis and machine learning algorithms, digital twins can identify subtle changes in equipment behaviour that may indicate an impending failure.
This allows timely intervention, preventing costly downtime, extending asset lifespan, and optimising maintenance schedules. Companies like Baker Hughes, a leading energy technology company, offer digital twin solutions that leverage AI and machine learning to optimise maintenance operations and enhance asset reliability.
Fine-Tuning for Peak Performance
Digital twins allow engineers to construct complex simulations of diverse production scenarios, facilitating the identification of optimal operating conditions and maximising output. This strategic approach yields substantial enhancements in efficiency and profitability. Schlumberger, a global technology provider for the energy industry, leverages digital twin technology to help its customers achieve significant production gains and cost reductions.
Enhancing Reservoir Management
Digital twins can create detailed reservoir models that simulate fluid flow, pressure changes, and production behaviour by integrating geological, geophysical, and production data. This enables engineers to identify optimal well placement, injection strategies, and production rates, leading to increased recovery factors and extended field life. Companies like Emerson Automation Solutions provide cutting-edge digital twin solutions for reservoir management, empowering oil and gas companies to make informed decisions and maximise hydrocarbon recovery.
Streamlining the Supply Chain Flow
Digital twins can provide end-to-end visibility into the supply chain, enabling companies to track the movement of products, optimise inventory levels, and anticipate potential disruptions. This results in improved efficiency, reduced costs, and enhanced customer satisfaction. IBM is a frontrunner in offering digital twin solutions for supply chain optimisation, helping oil and gas companies streamline their operations and achieve greater agility.
Safety First Risk Mitigation
Safety is of paramount importance in the oil and gas industry, and digital twins are playing a vital role in enhancing safety protocols and risk management strategies.
Empowering the Workforce Through Simulation
Digital twins can create immersive training simulations, providing workers with a safe and controlled environment to practice procedures and respond to emergencies. This approach significantly enhances worker competency, boosts confidence, and reduces the likelihood of accidents. Companies like Honeywell offer advanced simulation solutions that leverage digital twin technology to train oil and gas workers in a realistic and risk-free setting.
Proactive Risk Assessment and Mitigation
Digital twins can simulate various risk scenarios, enabling companies to identify vulnerabilities, assess potential impacts, and develop effective mitigation strategies. By adopting a proactive approach to risk management, oil and gas companies can prevent accidents, protect the environment, and safeguard their reputation. DNV GL, a global quality assurance and risk management company, is at the forefront of providing digital twin solutions for risk assessment and mitigation in the oil and gas industry.
Vision 2030 As A Digital Future for Oil and Gas
Saudi Arabia's ambitious Vision 2030 initiative envisions a diversified economy and reduced dependence on oil. However, the oil and gas industry remains a cornerstone of the economy, and the government is committed to ensuring its long-term sustainability and competitiveness through digital transformation. Digital twin technology is a key enabler of this vision.
Witness the Digital Twin Revolution at WAM Saudi
The upcoming World Advanced Manufacturing & Logistics Summit & Expo (WAM Saudi) will serve as a platform to showcase the transformative power of digital twins in the oil and gas industry. Attendees will have the opportunity to learn from industry leaders, network with peers, and explore the latest solutions and technologies driving this digital revolution.
As the oil and gas industry embraces the digital age, digital twin technology is proving to be a game-changer. By harnessing the power of digital twins, oil and gas companies can unlock new levels of efficiency, safety, and sustainability.
Join us at WAM Saudi 2024 to witness firsthand how digital twins are revolutionising the oil and gas landscape.
Register today and be part of the digital transformation